怎樣解決壓鑄件縮孔
壓鑄件在凝固過程中會發(fā)生體積收縮,形成縮孔、縮松;因鑄件內(nèi)部收縮,鑄件表面上會出現(xiàn)縮凹缺陷(見例圖)。對于壓鑄件來說,特別是厚大的壓鑄件,縮孔、縮松是普遍問題。本課題從如何對合金液的收縮進行補縮,如何阻礙合金液形成集中縮孔以及如何防止產(chǎn)生氣體、包卷氣體,如何排氣等幾個方面進行分析研究。以消除或減少縮孔、縮凹缺陷,從而提高壓鑄件的良品率。
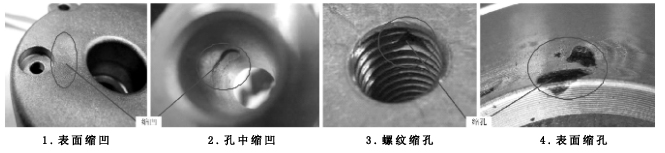
例圖
1、鑄件結(jié)構(gòu)改進
鑄件的壁厚越厚或熱節(jié)越大,休積的收縮量越大,就越難以把氣體排出,因此容易形成大的縮孔。這就要求盡量消除或減小鑄件的熱節(jié),把鑄件熱節(jié)部位尖角改為圓角;鑄件的壁厚要均勻,在鑄件壁厚相差較大的連接處,要逐步平緩過渡;如果鑄件設(shè)計不可避免熱節(jié)、凸耳、凸臺等,則可采用空心結(jié)構(gòu)、筋條結(jié)構(gòu)等來消除熱節(jié)和減輕鑄件質(zhì)量。
鑄件上較大的熱節(jié)部位、寬大的平面部位容易產(chǎn)生表面處理鋁合金壓鑄工藝 鋁合金壓鑄件渦流,因而容易包卷氣體;金屬液難以 充填到模具深腔,鑄件的盲孔、死角部位難以排氣、容易包卷氣體、易出現(xiàn)縮孔、縮凹缺陷 。設(shè)計該類鑄件時,就要考慮設(shè)置內(nèi)澆口和溢流排氣口的位置。
2、壓鑄模結(jié)構(gòu)改進
如果內(nèi)澆口截面積過小,會導(dǎo)致金屬液充填速度過快而產(chǎn)生噴射,促使金屬液包卷大量的氣體。因此要適當(dāng)加大內(nèi)澆口的截面積,防止內(nèi)澆口的金屬液過早凝固,從而堵塞增壓補縮通道,要增強內(nèi)澆口補縮能力和延長補縮時間。如果內(nèi)澆口的位置距離出現(xiàn)縮孔、縮凹的熱節(jié)位置比較遠,需適當(dāng)改變合金液導(dǎo)入內(nèi)澆口的位置、內(nèi)澆口的數(shù)量和內(nèi)澆口進入型腔的方向,以便合金液在型腔內(nèi)有序充填、壓力有效傳遞、型腔氣體有效排除,達到對熱節(jié)進行有效補縮的目的。
合理設(shè)計內(nèi)澆口與型腔連接的結(jié)構(gòu)形式,達到理想的內(nèi)澆口導(dǎo)流方向。要使合金液首先充填深腔、薄壁、需要較多合金液的位置、大平面的中間位置、鑄件表面質(zhì)量要求較高的位置、以及難以成形的位置等,使金屬液在型腔內(nèi)有序充填,防止金屬液產(chǎn)生渦流和卷氣。消除或減輕金屬液對型壁的正面沖擊,可以降低沖擊部位的模具溫度。注意改變內(nèi)澆口的流向或位置時,要防止金屬液過早凝固以致堵住分型面或排氣道。
比較小的熱節(jié)和非厚壁部位,可以設(shè)置在距商內(nèi)澆口較遠的位置,讓這些位置由一些較低溫度的合金液充填,這樣不會導(dǎo)致該部位的模具溫度過高。如在模具較深的型腔、死角、型腔中部等部位無法排氣或排氣不暢,可以采用排氣塞、頂桿、模塊鑲拼結(jié)構(gòu)排氣;用點冷卻加速厚壁部位合金液凝固速度;用點加熱提高薄壁部位模具溫度,使壓力有效傳遞;用改變充填流向消除渦流卷氣,以減小甚至消除鑄件縮孔。合理設(shè)置溢流槽、排氣槽位置、數(shù)目及尺寸,可以消除排氣不良的現(xiàn)象。
盡量減小機械加工余量;要使用型芯、抽芯鑄造出螺紋孔的底孔。如果壓室具有較小的充滿度,使用較低的壓射速度和足夠的壓射比壓,可以減輕壓鑄件的縮孔和縮凹。要選用合適的壓射室直徑,控制壓射室充滿度在30%-55%之間。
壓鑄件表面出現(xiàn)的輕度縮凹、粘模脫皮、小氣泡等缺陷,可以通過對模具表面進行噴丸、放電或打磨處理,使模具的表面變得粗糙,這樣有助于氣體排出,還可以增大模具的導(dǎo)熱效率,提高模具對合金液的冷卻速度。
如果模具的冷卻水管道距離內(nèi)澆口太近,由于內(nèi)澆口處的模具溫度過低,會導(dǎo)致內(nèi)澆口過早凝固,要使用冷卻水和模溫機,合理調(diào)節(jié)模具各部位的溫度。
如果模具溫度過高,雖然有利于補縮壓力傳遞,但會減緩合金液的凝固結(jié)晶速度,使熱節(jié)處形成較大縮孔。這就要在模具的橫澆道、內(nèi)澆口附近的型腔位置、型芯的高溫部位,以及鑄件的熱節(jié)部位,給模具內(nèi)部設(shè)計管道通冷卻水進行強制冷卻。壓鑄時對模具表面要多噴涂料及多吹氣冷卻,以降低模具過熱部位的溫度。
提高模具對合金液的冷卻效率,使合金液內(nèi)部和外部接近于同時凝固,讓合金液達到快速冷卻的效果,從而防止出現(xiàn)集中縮孔。
如果模具溫度過低,雖然能加快合金液的凝固速度,能消除或減小熱節(jié)處的凝固縮孔,但會過早地封閉補縮壓力的傳遞通道,影響補縮效果;也不利于涂料中水分快速去除,增加了合金液包卷氣體的幾率。這時在遠離內(nèi)澆口的熱節(jié)處不僅容易形成較大的縮孔,而且在鑄件內(nèi)部也會存在大量的氣孔,因此,要求在設(shè)計橫具時,要提高遠離內(nèi)澆口處、鑄件薄壁處、型腔深腔處、非主桿充填型腔處模具的溫度。一般是采用增加溢流槽的數(shù)量或增大其體積,電加熱管加熱,或模溫機通熱油等方法加熱模具。
為了消除熱節(jié)設(shè)計的鑄件空心結(jié)構(gòu),在模具上設(shè)置凸臺。起模斜度不能過大,否則會減小消除熱節(jié)的效果。另外,如果橫具使用中變形,產(chǎn)生了凸起部分,導(dǎo)致鑄件表面凹陷的,只要檢修模具、消除模具缺陷即可。
3、壓鑄工藝和合金熔煉改進
提高壓鑄機的壓射充填壓力和增壓補縮壓力,加大增壓閥的開度(縮短增壓的升壓時間),這樣可以及時進行增壓補縮,可以增加合金液的流動補縮能力,提高鑄件組織的致密度,可以通過降低低速、高速的壓射速度,推遲高速的開始位置來減少金屬液包卷氣體的含量。還可以采用很高的高速速度,使內(nèi)澆口速度達到60-120 m/s,讓金屬液呈霧狀噴射充填型腔,這樣雖然增加了鑄件中氣體的總含量,但不會包卷較大的氣泡,能明顯減小縮孔和縮凹尺寸,達到孔穴尺寸不超標(biāo)的目的。試驗得知,充填速度低會出現(xiàn)大氣孔,但數(shù)量少,總量也少;充填速度高,出現(xiàn)氣孔的數(shù)量多,總量也多,但尺寸小。
較高的低速速度,不平穩(wěn)的低速速度,以及過早開始啟動高速速度,都會使金屬液在壓射室及橫澆道里出現(xiàn)紊流而產(chǎn)生卷氣。壓鑄合金熔化或澆注溫度越高,引起合金內(nèi)部吸氣越多、鑄件結(jié)晶的晶粒越大,合金液凝固后的收縮率越大。在合金液的熔化和保溫過程中需控制合金液的溫度不要過熱,并要使合金液處于高溫的時間不要過長。
如果合金液需要超過2h的停產(chǎn)保溫, ADC12鋁合金的保溫溫度要降至620-630 ℃。在保證鑄件不產(chǎn)生冷隔、澆不足的前提下,要盡量降低合金液的澆注溫度,這樣可以減少合金液的收縮量和含氣量。
空氣中的水分、爐料中的水分和油污里的有機物等,在高溫時會分解出氫原子。 Al、Zn、Mg等合金液,隨著溫度的升高,會吸附溶解更多的氧原子。同時在合金液的氧化夾渣和夾雜物團粒中,也容易吸附氫原子,在合金液凝固的過程中,會使附著的氫原子自動脫離凝固體而進入到液體之中。當(dāng)液體之中的氫原子聚集富余之后,由于溫度降低,氫原子相互結(jié)合形成氫氣富集的氫氣產(chǎn)生膨脹壓力,又促進了液體的補縮流動,同時也促使合金液中形成較大的氣縮孔。因氯原子會附著在氧化夾渣和雜質(zhì)上,僅靠除氣精煉解決不了,還要仔細地對合金液進行徹底的除渣精煉操作,這樣才能較好地降低合金液的含氣量和雜質(zhì)含量。
合金液中某些化學(xué)成分如果超差,會增大合金的體積收縮率,如鋁合金中的Zn含量增加就會增大合金的體積收縮率,因此要對合金液進行常規(guī)檢查,控制、調(diào)整好化學(xué)成份,并適當(dāng)?shù)乜刂苹貭t料的用量比例。
用密度檢測儀檢測樣塊,并觀察樣塊的凝固凹陷程度,觀察合金液的收縮量和含氣量。一般結(jié)晶溫度范圍大的合金容易出現(xiàn)集中縮孔,其鑄件容易出現(xiàn)漏氣,而一般結(jié)晶溫度范圍小的合金,則容易出現(xiàn)分散的縮孔,其鑄件不容易出現(xiàn)漏氣。為了提高鑄件的密度,可以對合金液進行變質(zhì)處理,在鋁合金液中添加0.15%-0.20%的Ti、Sr等晶粒細化劑,能減輕合金的縮孔傾向。必要時就需要改用體收縮率、線收縮率小的合金品種。
如果鑄件的內(nèi)澆口斷面出現(xiàn)縮孔、影響因素較多。解決的方法有:
為使壓力更好地傳遞,適當(dāng)改進澆注系統(tǒng),加大內(nèi)澆口截面積,加大內(nèi)澆口厚度,防止因內(nèi)澆口過早凝固而影響壓力的傳遞;如果橫澆道比內(nèi)澆口冷卻收縮快,會使內(nèi)澆口處金屬液倒流到橫澆道,結(jié)果使鑄件在內(nèi)澆口處形成縮孔,這時就要減小內(nèi)澆口厚度,給內(nèi)澆口部位進行充分冷卻;提高增壓壓力;消除金屬液在壓射時產(chǎn)生的飛料和飛邊毛刺;加大增壓上升速度閥的開度;延長增壓持壓時間到澆口完全凝固為止;對金屬液精煉處理減少含氣量,降低金屬液的澆注溫度,減少金屬液的收縮等,這些都可以減小或消除內(nèi)澆口處的縮孔。
采用半固態(tài)壓鑄工藝,該工藝是將具有固相率3%-50%的合金漿料,壓射充填到型腔內(nèi),雖然在合金漿料內(nèi)部已經(jīng)有固相顆粒存在,能夠加速合金凝固,消除大的縮孔,但因為還有部分處于液態(tài)的合金,在結(jié)晶時存在體積收縮,最終還會出現(xiàn)小的縮孔或縮松,不過,半固態(tài)壓鑄比液態(tài)壓鑄出現(xiàn)的縮孔、縮松尺寸小,數(shù)量要少很多。
4、壓鑄操作改進
壓鑄的余料料餅厚度過薄,會影響增壓壓力的傳遞,使壓射最終的增壓起不到有效的補縮作用,所以要采用定量澆注,確保壓鑄的料餅厚度。給型腔噴涂脫橫劑的量過多,涂料發(fā)氣量大,涂料濃度高,涂料的水分在澆注前未蒸發(fā)干凈,都會促使產(chǎn)生大雖氣體卷入金屬液,如果氣體被壓縮在型腔表面與金屬液界面之間,在鑄件皮下出現(xiàn)大的氣孔,在鑄件表面就會出現(xiàn)縮凹。
受到涂料的氧化、污染的氣縮孔、空穴的內(nèi)壁表面多呈暗灰色。這就要求涂料的濃度低、用量少、噴涂均勻;噴涂料后要用壓縮空氣把型腔表面的水分吹干。讓水分揮發(fā)干凈后再合模;提高模具溫度,使涂料水分能多快速地蒸發(fā)掉;必要時,還可以改用發(fā)氣小的涂料。
無論是油劑、水劑或固體顆粒狀的沖頭潤滑涂料,如果使用量過多,都會在遇到高溫合金液時產(chǎn)生大量氣體,部分氣體進入金屬液后不能及時排出;未燃燒盡的涂料微粒進入合金液后,還會繼續(xù)燃燒產(chǎn)生氣泡微粒。氣泡微粒與合金液混合,更難以排出。所以一定要定時點檢,控制好沖頭潤滑劑的用量。
如果內(nèi)澆口的斷面有氣孔或有灰黑色、黃黑色的夾渣,是沖頭涂料、模具涂料、沖頭漏水等遇到金屬液后在壓射室產(chǎn)生大量的氣體和氧化夾渣進入合金液,污染了壓射室里的合金液,使金屬液含有大量的氣體,特別明顯的表現(xiàn)是在壓鑄件內(nèi)澆口的斷面會呈現(xiàn)氣孔和氧化夾渣,在整個鑄件的內(nèi)部斷面,也會呈現(xiàn)這些缺陷。
其關(guān)鍵的原因:
一、沖頭涂料太多
二、是沖頭漏水到壓射室
三、是橫具涂料水噴進了壓射室里,所以一定要定時點檢,不讓壓射室里進入水分
如果鑄件表面上呈現(xiàn)松散不緊實的宏觀組織,這時在熱節(jié)處出現(xiàn)縮凹。這是因為模具的溫度太低,需要適當(dāng)提高模具溫度和合金液的澆注溫度,減少涂料的用量,提高壓射比壓,或是因為型腔噴涂涂料后,多余的涂料水分沒有吹干,型腔中產(chǎn)生了大年的氣體所致,同時鑄件表面還會發(fā)黑。
對出現(xiàn)縮孔、縮凹部位的模具表面,可以用多噴涂涂料來降低模具局部的溫度;也可以用冷卻水管、定點定時地對模具的局部表面噴灑冷卻水,來降低模具的溫度,但容易引起模具壽命縮短。
如果模具表面或型芯表面,受到合金液的沖擊而過熱,或在鑄件的熱節(jié)部位而過熱,模具表面會粘一層壓鑄合金,這層壓鑄合金會阻礙金屬液在結(jié)晶凝固時熱量的快速散發(fā)和傳遞,增加了鑄件出現(xiàn)縮孔、縮松的幾率。
這時除了清理、拋光模具表面粘結(jié)的合金、對模具進行氮化處理之外,關(guān)鍵是要在模具過熱部位設(shè)置冷卻水管道,通水冷卻來降低過熱部位的橫具溫度。
5、強制補縮法
強制補縮是使用外力推動液態(tài)、半固態(tài)及固態(tài)的金屬移動進行補縮。外力實現(xiàn)鑄件的強制補縮有兩種方法:
1.局部擠壓
2.鍛壓補縮
采用先壓鑄充型,后擠壓補縮或模鍛補縮的工藝,是解決鑄件縮孔、縮松缺陷的有效途徑。在壓鑄工藝的基礎(chǔ)上,增設(shè)強制的局部擠壓補縮,是能夠與壓鑄工藝特點相適應(yīng)的,能很好地解決壓鑄件局部的縮孔、縮松問題。
6、結(jié)語
縮孔、縮松缺陷,主要是由于合金液結(jié)晶時的體積收縮,合金液中包卷的氣體和合金液溶解的氫原子析出后的氣體形成的,主要的措施是要設(shè)計出沒有熱節(jié)的、易于充填的鑄件;設(shè)法加快合金的收縮,降低熱節(jié)部位的模具溫度;精煉合金液,減少合金液充填型腔時包擠壓鑄造是在外擠壓力下凝固的近凈成形工藝。
外擠壓力可以促使凝固的鑄件與模具緊密接觸,增加了鑄件/模具間的傳熱,從而得到組織細化和枝晶間距較小的凝固組織,使鑄件具有良好的力學(xué)性能,因此,該工藝也特別適用于高品質(zhì)的安全結(jié)構(gòu)件的生產(chǎn)。
在擠壓過程中,外擠壓力不僅改變了鑄件/模具界面的接觸情況,而且改變了液相線溫度。從而改變了鑄件的傳熱與溫度分布。同時,固相形成和凝固收縮對來自沖頭的壓力傳遞也具有重要影響,因此,熱力相互作用行為是擠壓鑄造的本質(zhì)問題之一。對此,一些研究者利用數(shù)值橫擬方法進行了研究,但是,由于高溫和外力作用下型腔內(nèi)壓力測試的難度與復(fù)雜性,僅壓鑄過程壓力變化的測試與分析有少量報道,而擠壓鑄造相關(guān)研究工作尚未見報道,因此,已有數(shù)值模擬研究只能通過縮孔缺陷進行間接驗證,缺少試驗壓力測試的直接對比。
『不是原創(chuàng),來自于互聯(lián)網(wǎng)』