泵體的熔模鑄造工藝
針對外形尺寸較大、形狀復雜的泵體鑄件,通過制作水溶性芯子和蠟模組裝的方式,成功制作了泵體蠟模。采用硅溶膠工藝制殼,設計合理的澆注系統(tǒng),確定合理的脫蠟工藝和澆注工藝,成功澆注出該泵體鑄件。
泵類產(chǎn)品被廣泛應用于輸送各種流體,為保證性能,對泵體內(nèi)壁流道部分尺寸精度和表面杠經(jīng)度要求較高,對泵體本身承壓值和外觀質(zhì)量也有較高的要求。熔模鑄造由于受其工藝特性的局限,一般鑄件質(zhì)量只有幾克到幾公斤。對于尺寸較大,形狀復雜的鑄件,無論從壓制蠟模還是制殼等工藝環(huán)節(jié),都存在一定的難度。
舉例:一批泵體(鑄件毛坯),外形尺寸為 515mm ×410 mm,質(zhì)量為 47.85 kg,材質(zhì)為 CF8M,見圖1。經(jīng)過周密設計,采用合理的工藝方案,成功生產(chǎn)出了這批泵體鑄件。
1.1制作尿素芯
受泵體本身結構特點影響,泵體內(nèi)腔不可能直接由模具壓出,根據(jù)生產(chǎn)實際,采用尿素芯工藝,由于泵體流道部分尺寸精度和表面粗糙度全部由尿素芯決定,因此尿素芯的制作要求嚴格,尿素與白砂糖產(chǎn)格按照(質(zhì)量比) 100:5混合后加熱至130~150℃,溶化后灌入內(nèi)腔已均勻涂抹好松節(jié)油的模型中,完全冷卻后取出尿素芯檢查,要求尿素芯呈白色,表面光潔無缺陷,尺寸合格。
1.2蠟模制作
壓蠟溫度為54~60℃,壓射壓力為0.8~1.0MPa,壓射時間為50s,保壓時間為10min,法蘭盤單獨壓蠟后組焊粘結。要求蠟模表面與內(nèi)腔表面光潔,無流紋,側面大法蘭盤與底面垂直,和對側12個凸臺面平行,必要時需進行整形。
1.3 流注系統(tǒng)設計
(1)方案1 注入方式為冒口頂注式
(2)方案2 注入方式為聯(lián)合注入式

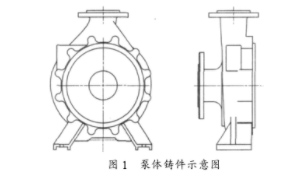
一、蠟模制作
1.1制作尿素芯
受泵體本身結構特點影響,泵體內(nèi)腔不可能直接由模具壓出,根據(jù)生產(chǎn)實際,采用尿素芯工藝,由于泵體流道部分尺寸精度和表面粗糙度全部由尿素芯決定,因此尿素芯的制作要求嚴格,尿素與白砂糖產(chǎn)格按照(質(zhì)量比) 100:5混合后加熱至130~150℃,溶化后灌入內(nèi)腔已均勻涂抹好松節(jié)油的模型中,完全冷卻后取出尿素芯檢查,要求尿素芯呈白色,表面光潔無缺陷,尺寸合格。
1.2蠟模制作
壓蠟溫度為54~60℃,壓射壓力為0.8~1.0MPa,壓射時間為50s,保壓時間為10min,法蘭盤單獨壓蠟后組焊粘結。要求蠟模表面與內(nèi)腔表面光潔,無流紋,側面大法蘭盤與底面垂直,和對側12個凸臺面平行,必要時需進行整形。
1.3 流注系統(tǒng)設計
該鑄件需進行氣壓試驗,內(nèi)部不允許有縮孔縮松等缺陷,考慮到正面12個凸臺及出水口根部為熱節(jié)部位,在鑄件以上部位適當增加了補縮冒口。針對該鑄件的結構特點,設計了兩套流注系統(tǒng)方案。
(1)方案1 注入方式為冒口頂注式
采用組焊的十字型模頭,長度由鑄件確定,澆道寬度為55mm,澆道厚度為50mm,流口杯尺寸為Φ30 mm xΦ90mm ×180 mm,見圖2(a) 。
(2)方案2 注入方式為聯(lián)合注入式
在方案1的基礎上,在泵體底端加一側澆道及澆口杯,連接到底面法蘭盤,見圖2(b)。

二、制殼
為確保型殼強度和鑄件表面粗糙度,采用硅溶膠工藝,具體工藝參數(shù)件見表1和表2。
由于該鑄件體積較大、壁厚不均,如果采用普通脫蠟方法脫蠟,型殼由于受熱不均勻會出現(xiàn)鼓脹、開裂等問題,因此必須改進脫墻工藝實現(xiàn)順序脫蠟。
具體做法為:用3層廢報紙包住泵體型殼,使冒口及澆道外露,這樣澆注系統(tǒng)的蠟模先受熱熔化流出,為泵體蠟模的流出形成通道,從而實現(xiàn)順序脫蠟。脫蠟壓力為0.6~0.75 MPa,脫蠟時間為25~30 min,脫蠟后型殼狀況良好。
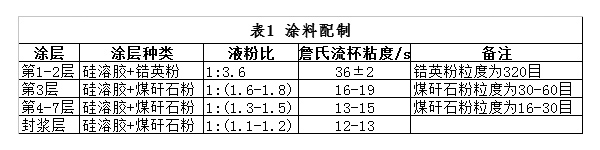
三、型殼培燒及澆注
具體澆注工藝為:首先采用一側澆口杯先將鋼水澆至鑄件整體2/3處,再用中間流口杯將鋼水澆滿,型殼出爐溫度大于950 ℃,鋼水澆注溫度為1620~1630℃,澆注時間為120s,為防止縮松,澆注完畢后30s內(nèi)在冒口處補充鋼水并加蓋保溫劑。在鑄件冷卻過程中,往凸臺及出水口根部熱節(jié)處進行局部水淬。
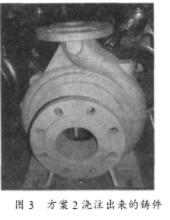
具體做法為:用3層廢報紙包住泵體型殼,使冒口及澆道外露,這樣澆注系統(tǒng)的蠟模先受熱熔化流出,為泵體蠟模的流出形成通道,從而實現(xiàn)順序脫蠟。脫蠟壓力為0.6~0.75 MPa,脫蠟時間為25~30 min,脫蠟后型殼狀況良好。
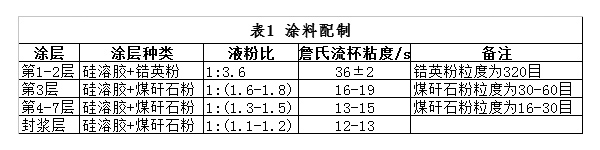
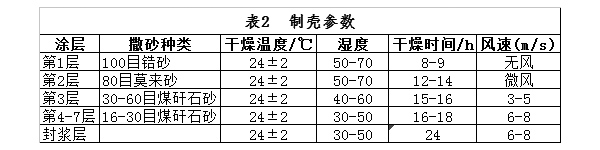
三、型殼培燒及澆注
因為型殼體積及鑄件壁厚都較大,為確保型殼培燒質(zhì)量,應適當提高培燒溫度,并延長保溫時間。采用的培燒溫度為1080~1100℃,培燒時間為1h。采用方案1澆注后,鑄件出水口根部熱節(jié)處縮孔、縮松嚴重。采用方案2澆注出來的鑄件品質(zhì)良好(見圖3)。
具體澆注工藝為:首先采用一側澆口杯先將鋼水澆至鑄件整體2/3處,再用中間流口杯將鋼水澆滿,型殼出爐溫度大于950 ℃,鋼水澆注溫度為1620~1630℃,澆注時間為120s,為防止縮松,澆注完畢后30s內(nèi)在冒口處補充鋼水并加蓋保溫劑。在鑄件冷卻過程中,往凸臺及出水口根部熱節(jié)處進行局部水淬。
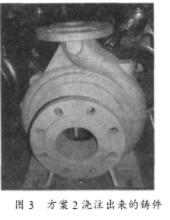
四、結語
通過合理的設計蠟模制作工藝及制殼工藝,制造出較大泵體型殼。采用順序脫蠟的方法,有效防止了型殼的鼓脹、開裂,采用改進后的澆注系統(tǒng)方案,鑄件清理后無縮孔、縮松現(xiàn)象,鑄件無明顯變形,經(jīng)檢查,表面品質(zhì)達到用戶要求,尺寸合格,氣壓試驗合格。
『不是原創(chuàng),摘自互聯(lián)網(wǎng)』